현대자동차가 자동차 도장 공정에서 에너지 소비를 획기적으로 줄여 탄소 배출을 저감하는 새로운 도장 기술을 개발했다고 30일 밝혔다.
자동차 도장 공정은 크게 전처리, 하도도장, 중도도장, 상도도장 등 네 단계를 거치는데, 이 과정에서 고온 처리를 통해 입혀진 도료를 단단하게 굳히는 공정을 ‘경화 공정’이라고 한다.
해당 공정은 기존 140℃에서 이뤄졌으나 새로 개발된 기술을 사용하면 90℃까지 온도를 낮출 수 있다.
이는 도료 성분 차이로, 기존 도료는 140℃ 이상에서만 경화되는 ‘멜라민’이 사용됐으나 신규 도료 소재인 ‘이소시아네이트’를 사용하면서 비교적 낮은 온도에서도 사용이 가능해졌다.
이에 따라 도료 도장 과정에서의 에너지 소모를 줄여 결과적으로 탄소 배출을 저감할 수 있다고 현대자동차는 밝혔다.

실제로 도장 공정은 자동차 제조 공정 중 가장 많은 비율인 43%의 에너지를 소모하며, 그만큼 탄소 배출도 가장 많은 공정으로 꼽힌다.
현대자동차는 이번 도료 기술이 상용화될 경우 탄소 배출과 가스 사용량 모두 40%가량 절감할 수 있을 것으로 전망했다.
특히 향후 모든 현대차 공장이 신기술을 적용하면 한 해 자동차 제조에서 배출하는 이산화탄소를 16,000t 이상 저감할 수 있다.
이는 소나무 2백만 그루를 심는 것과 같은 효과가 있다고 현대자동차는 전했다.
또 저온 경화 기술은 탄소 저감뿐만 아니라 도장 품질 향상에도 큰 효과가 예상된다.
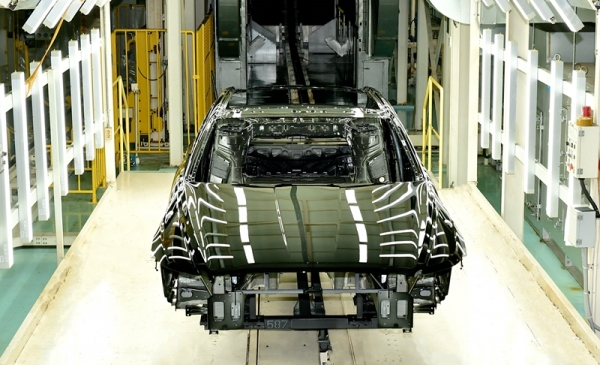
기존 고온 경화 공정에는 차체만 도장이 가능해 플라스틱 범퍼 등 기타 부품을 도장하기 위한 추가적인 작업이 필요했으나, 이번에 개발된 저온 공정은 대부분 제품에 적용할 수 있다.
현대차는 현재 울산 5공장에 신기술을 시범 적용 중이며, 향후 기술의 전면적인 사용을 검토하고 있다고 밝혔다.
현대차 관계자는 “도장 공정에서 에너지 소모를 획기적으로 저감하는 기술 개발을 통해 현대차의 2045년 탄소 중립 목표에 한 발 더 다가갈 수 있을 것”이라고 전했다.